An Unbiased View of Alcast Company
An Unbiased View of Alcast Company
Blog Article
9 Easy Facts About Alcast Company Explained
Table of ContentsOur Alcast Company IdeasThe Ultimate Guide To Alcast CompanyThe Definitive Guide for Alcast CompanyThe Facts About Alcast Company UncoveredThe Best Strategy To Use For Alcast CompanyRumored Buzz on Alcast Company
Chemical Comparison of Cast Aluminum Alloys Silicon advertises castability by lowering the alloy's melting temperature and boosting fluidness during spreading. In addition, silicon contributes to the alloy's stamina and use resistance, making it important in applications where toughness is vital, such as automobile components and engine components.It also boosts the machinability of the alloy, making it much easier to process right into completed items. In this way, iron adds to the total workability of aluminum alloys. Copper boosts electric conductivity, making it useful in electrical applications. It additionally improves corrosion resistance and adds to the alloy's general toughness.
Manganese adds to the toughness of light weight aluminum alloys and enhances workability (Aluminum Casting). It is typically utilized in functioned light weight aluminum items like sheets, extrusions, and accounts. The visibility of manganese help in the alloy's formability and resistance to breaking throughout manufacture procedures. Magnesium is a lightweight aspect that gives stamina and influence resistance to light weight aluminum alloys.
How Alcast Company can Save You Time, Stress, and Money.
Zinc improves the castability of light weight aluminum alloys and helps control the solidification process during casting. It boosts the alloy's toughness and solidity.
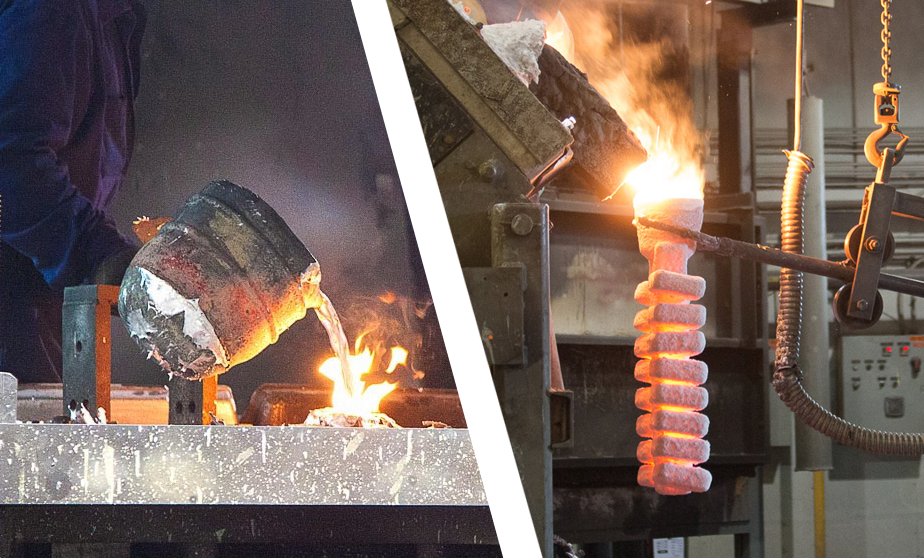
The key thermal conductivity, tensile stamina, return strength, and elongation differ. Amongst the above alloys, A356 has the greatest thermal conductivity, and A380 and ADC12 have the most affordable.
The Ultimate Guide To Alcast Company

In precision casting, 6063 is well-suited for applications where complex geometries and top quality surface area coatings are extremely important. Instances consist of telecommunication rooms, where the alloy's premium formability enables sleek and aesthetically pleasing layouts while keeping architectural integrity. In a similar way, in the Illumination Solutions market, precision-cast 6063 components create stylish and effective lights fixtures that require complex shapes and excellent thermal efficiency.
The A360 exhibits exceptional elongation, making it optimal for complex and thin-walled parts. In accuracy casting applications, A360 is fit for markets such as Consumer Electronics, Telecommunication, and Power Tools.
Alcast Company Things To Know Before You Buy
Its special homes make A360 an important option for precision spreading in these industries, boosting item resilience and quality. Casting Foundry. Aluminum alloy 380, or A380, is a widely used casting alloy with a number of distinctive qualities.
In precision casting, aluminum 413 beams in the Customer Electronics and Power Equipment sectors. This alloy's remarkable corrosion resistance makes it an exceptional choice for outside applications, guaranteeing lasting, sturdy products in the pointed out sectors.
7 Simple Techniques For Alcast Company
When you have actually chosen that the aluminum pass away casting process is ideal for your project, a crucial following step is picking one of the most appropriate alloy. The light weight aluminum alloy you pick will substantially influence both the casting procedure and the buildings of the end product. Because of this, you need to make your choice carefully and take an educated technique.
Identifying the most suitable aluminum alloy for your application will certainly suggest evaluating a wide range of qualities. The initial group addresses alloy attributes that affect the production process.
What Does Alcast Company Do?
The alloy you select for die casting straight affects numerous aspects of the spreading look at more info process, like just how simple the alloy is to collaborate with and if it is susceptible to casting defects. Hot cracking, additionally referred to as solidification fracturing, is a common die casting defect for light weight aluminum alloys that can lead to internal or surface-level splits or cracks.
Specific light weight aluminum alloys are extra susceptible to hot fracturing than others, and your selection ought to consider this. It can damage both the cast and the die, so you must look for alloys with high anti-soldering homes.
Corrosion resistance, which is already a significant feature of light weight aluminum, can differ considerably from alloy to alloy and is a vital characteristic to think about depending upon the ecological conditions your product will be subjected to (Aluminum Casting). Wear resistance is another building generally looked for in aluminum items and can set apart some alloys
Report this page